Like Results? Start with STANDARD WORK.
- March 19, 2018
- Posted by: Nayte Carrick
- Category: Uncategorized
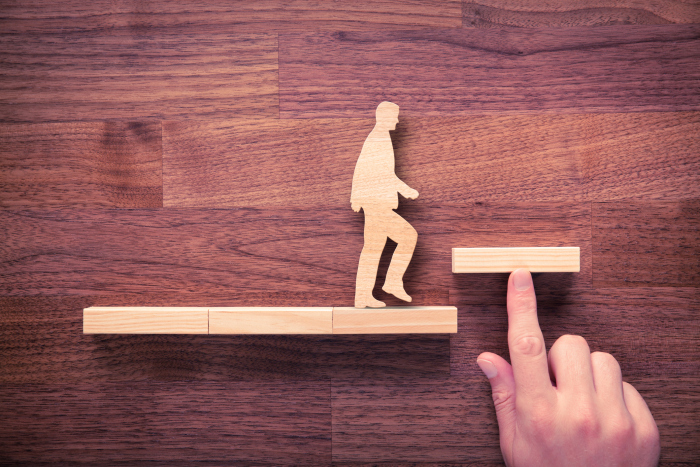
What is Standardized Work?
Standard work is an important component of the Lean methodology, forming the baseline for continuous improvement through the documentation of current best practices. Each time the standard is improved, the new standard becomes the basis for future improvements.
It is important for standard work to be documented and to show
- Clear, appropriately detailed, outlines of each process and task
- The current best practice
- Key points critical to safety, quality, and performance
- Explanations for why things are done a certain way
Standard work is an effective method of improving quality and consistency, reducing waste, and providing maximum value to customers. Although it seems to be a simple concept, it only works when deployed, communicated, and managed well – an effective standardized work system is about more than just creating documents.
The idea of standard work originated in the manufacturing sector with the observations of early industrial engineers like Frederick W. Taylor. Today, it and the other Lean tenets are used by a variety of companies seeking to improve.
The fact that the approach is popular with organizations of all types and sizes is evidence to the fact that the results are worth the effort.
How Does It Work?
The implementation of standard work requires:
- The identification of the most efficient and effective practices, as well as the standard time needed to complete those practices.
- The documentation of the best practices using not only text, but images or diagrams as well (or sometimes video!)
- The availability of the documents in the place where the work is being done
- The education of each employee about both how the standard work should be performed and the reasons behind what are called “key points” in the process.
There are also three essential elements for the implementation of standard work
- Takt time – “Takt” is a German word referring to the tempo or beat of a piece of music. In Lean, it describes the rate at which products must be produced to meet customer demand.
- The exact sequence employees follow to complete a specific task.
- The standard amount of “work in process” (WIP) inventory – components, applications, data inputs, etc. – that’s required to perform a given task.
What Are the Benefits of Standardized Work?
There are many benefits to this practice. For example:
- Reduced risk of injuries, ergonomic problems, or other safety issues
- Quality, consistency, and the elimination of errors
- Reduced waste and increased productivity
- Simplified new employee training and clear employee expectations
- Reduced dependence on individual skill holders
- Instant visibility into process breakdowns, simplifying decision making
- Predictable costs and on-time delivery
Standard Work Dos and Don’ts
DO engage the employees who actually do the work in the standardized work development process. Engineers and other outsiders may certainly be involved in the process, but the most important input comes from the frontline employees.
DO document the existing process, but keep an open mind and look for opportunities for improvement.DOkeep standardized work as simple as possible, breaking each task into its smallest steps. Paying attention to the smallest steps can help prevent variation.
DO document the process to an appropriate degree of detail.
DO make sure that documentation is easy to understand. The inclusion of diagrams, examples, or other visual materials will help with this.
DO be sure that your standard work documentation is clearly displayed in the workplace, rather than being hidden in a binder or a computer.
DO provide a structured methodology for improving the process.
DON’T just document the current best practices without looking for opportunities to improve them.
DON’T think about standardized work creation as a one-time event; it should be continually refined over time.
DON’T write the document in a way that is overly rigid, given the situation. Standardized work is not meant to be a substitute for thinking and judgment when the work or customer needs call for it.
DON’T change procedures or processes without updating the standardized work. Doing so will cancel out the positive impact of standardized work.
DON’T create a complex procedure for changing standardized work. If the process is too complicated, people will avoid making any such changes.
DON’T allow unnecessary variation from the standardized work. If the standardized work truly defines the best practice, it should be performed the same way every time and performed the same way by other people. Otherwise, it should be changed.